In recent years, the VESNA Smart Greenhouse project has become a part of research and education at our Institute of Information Engineering, Automation, and Mathematics, Faculty of Chemical and Food Technology STU in Bratislava. The initial version of the project provided ample opportunities for students to learn about data analysis, complex system control, and hardware problem-solving, see here. However, the initial version had many imperfections that presented challenges in solving numerous problems, and there was a lot of room for improvement. Therefore, the development of this project did not come to a halt, and a new and improved version has recently been introduced, which offers numerous innovative features. The latest iteration has undergone comprehensive improvements in all aspects, ranging from design to sensory equipment and the electronic control unit itself.
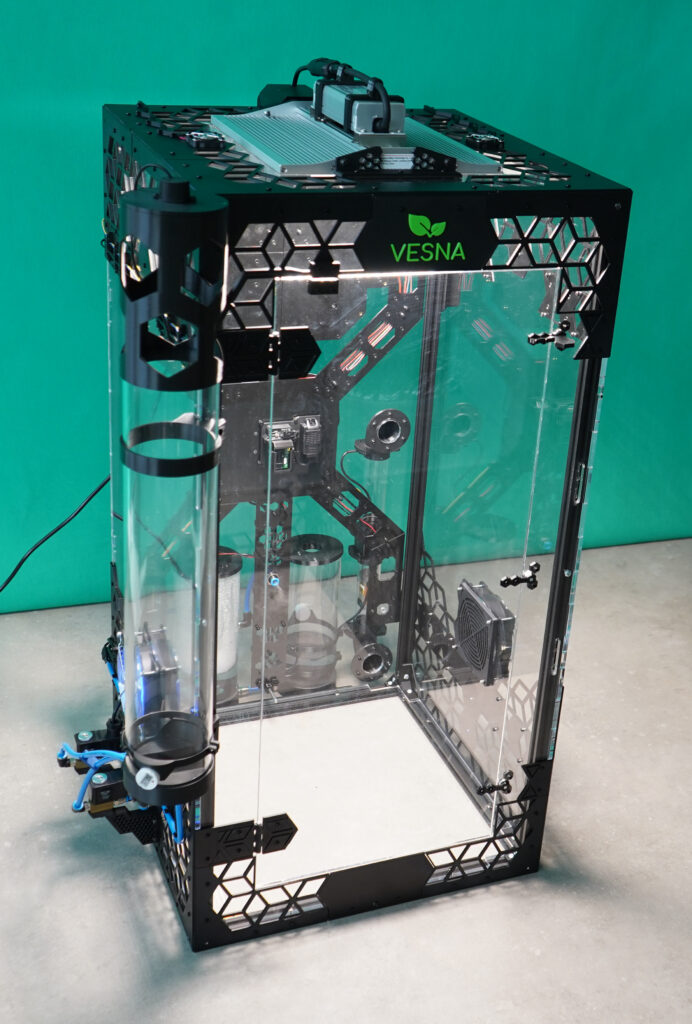
Upon first glance, it is evident that the design of the smart greenhouse is more intricate, sophisticated, and structurally robust. Additionally, an irrigation or humidification system has been integrated into the greenhouse, and that is not all.
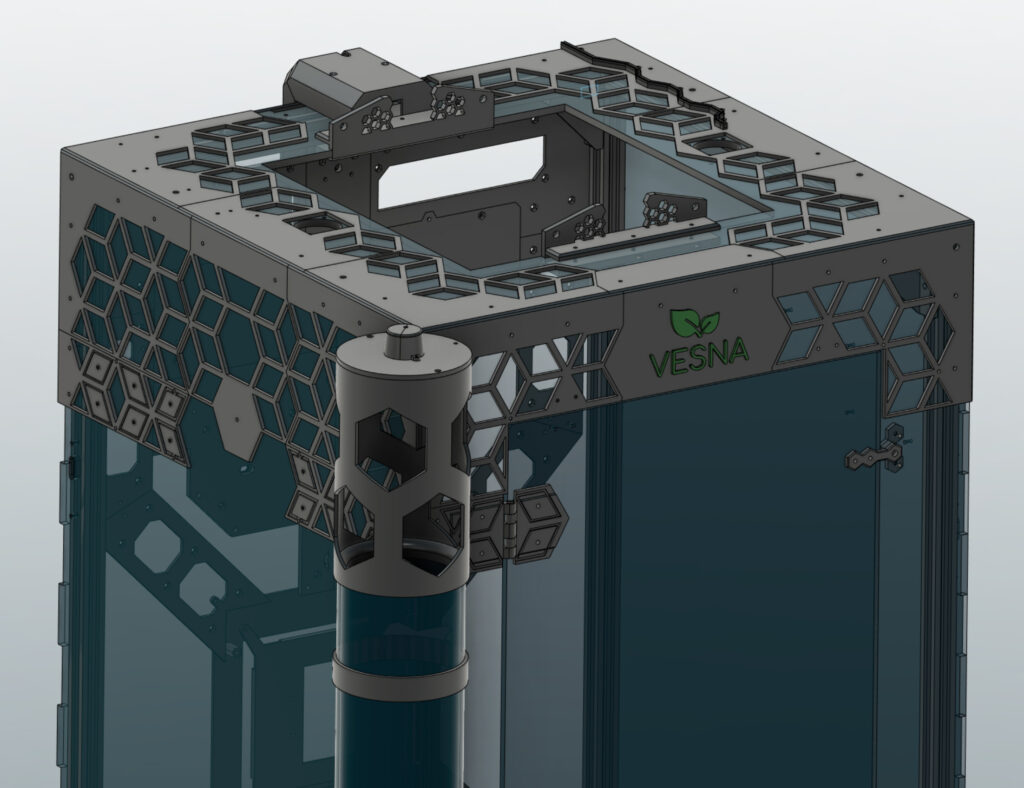
The structure’s frame is constructed from extruded aluminum profiles, which are more practical and straightforward to assemble. The walls are filled with 6 mm thick acrylic, and ornamental black features, primarily for design purposes, are printed from PETG and PLA+ materials on our 3D printers. All parts have been designed from the sketch as a 3D model and subsequently 3D printed on PRUSA MK3S+.
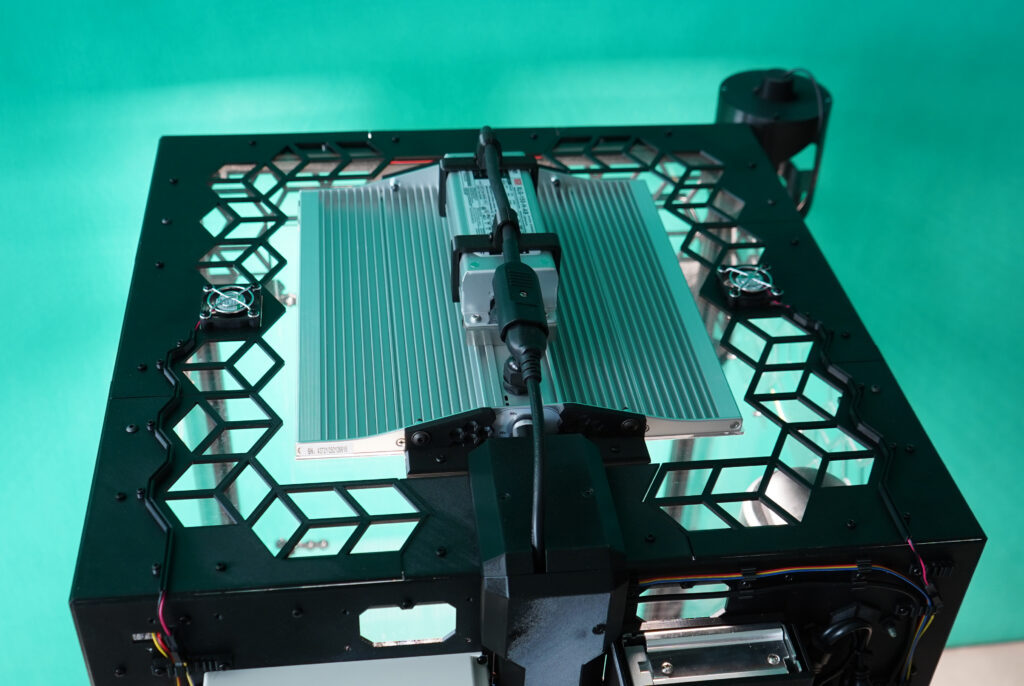
Another notable innovation is the lighting system. The greenhouse’s lighting features the full spectrum of wavelengths required by the plants, and its intensity can be adjusted from 0 to 100%. To dissipate the heat generated by the lights, two fans have been placed on either side of the lighting. Further details about actuators and sensors are listed here.
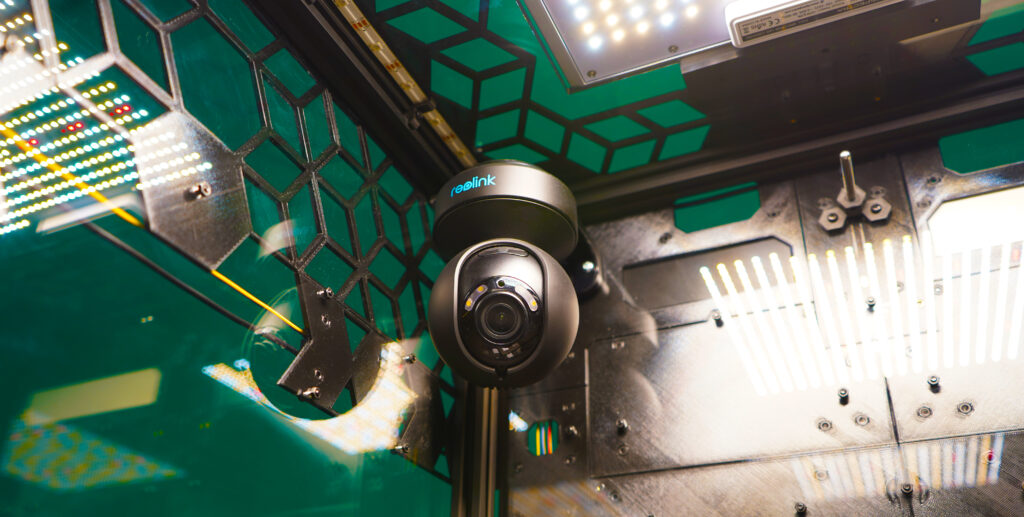
In addition, a waterproof camera with a WiFi connection was installed to capture images of the plant and its development. Based on these images, a machine learning algorithm can be trained to detect the plant’s growth stage, condition, and potential diseases.

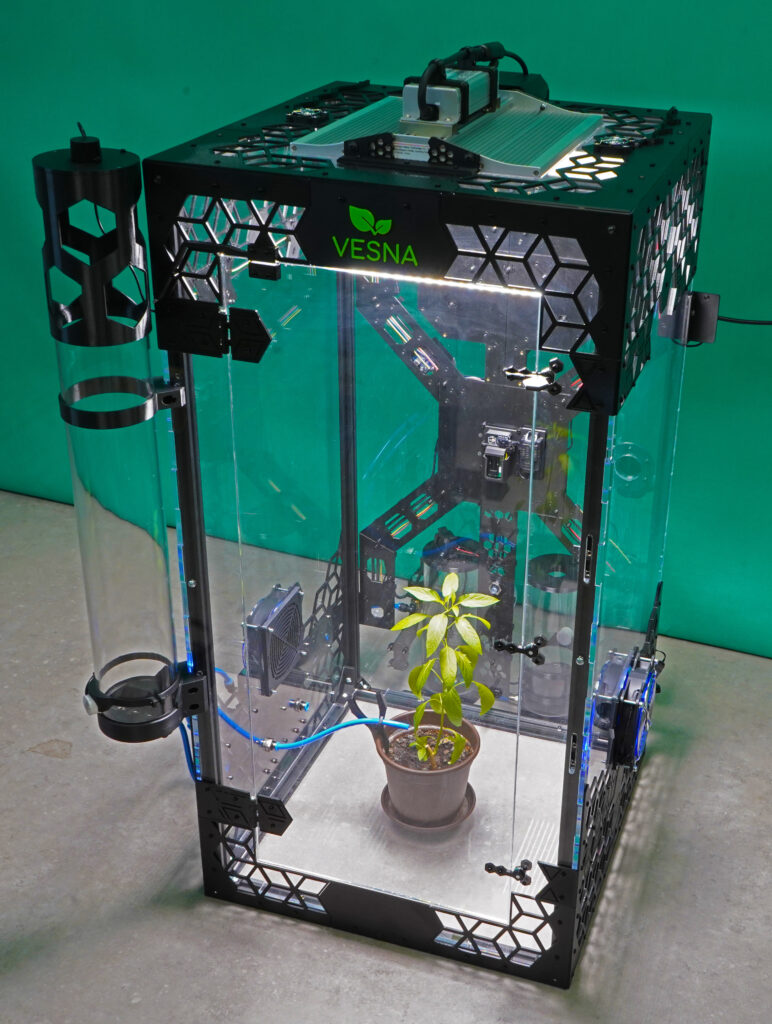
The greenhouse’s front section is equipped with a magnetic door and a sensor that detects when the door is open. The air circulation in the greenhouse is facilitated by two 120 mm PWM fans, which produce an airflow of 82,91 m3 per hour and feature blue backlighting. The fan’s speed can be adjusted infinitely to suit the needs of the plants.
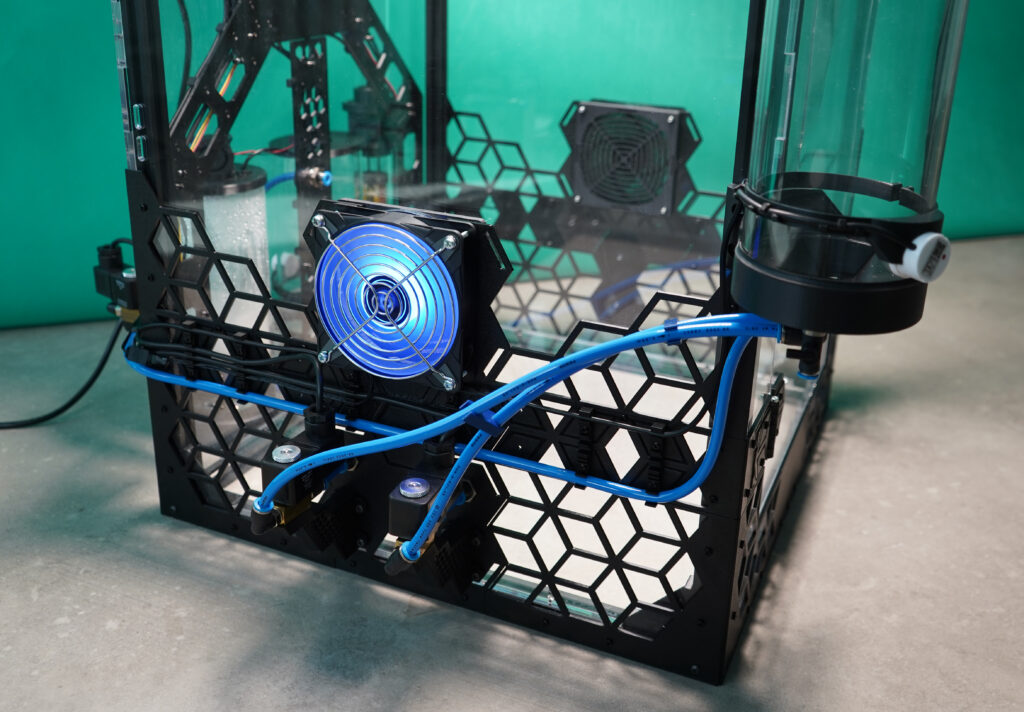
The left side of the greenhouse features an irrigation unit comprising an acrylic tank and two valves. The tank has two sensors: a non-contact liquid sensor that signals when the tank is empty and requires a refill, and an ultrasonic distance sensor that measures the level height. The liquid flow rate and, therefore, the volume of water used for watering the plants is influenced by the level height. Since self-priming watering is done through an open valve, it is crucial to know the level height and valve characteristics to determine the length of time the valve will remain open accurately. This ensures that the desired volume of water is used for watering the plants. Thus, this is the first dynamic system of the greenhouse, which is comparatively simpler than others.
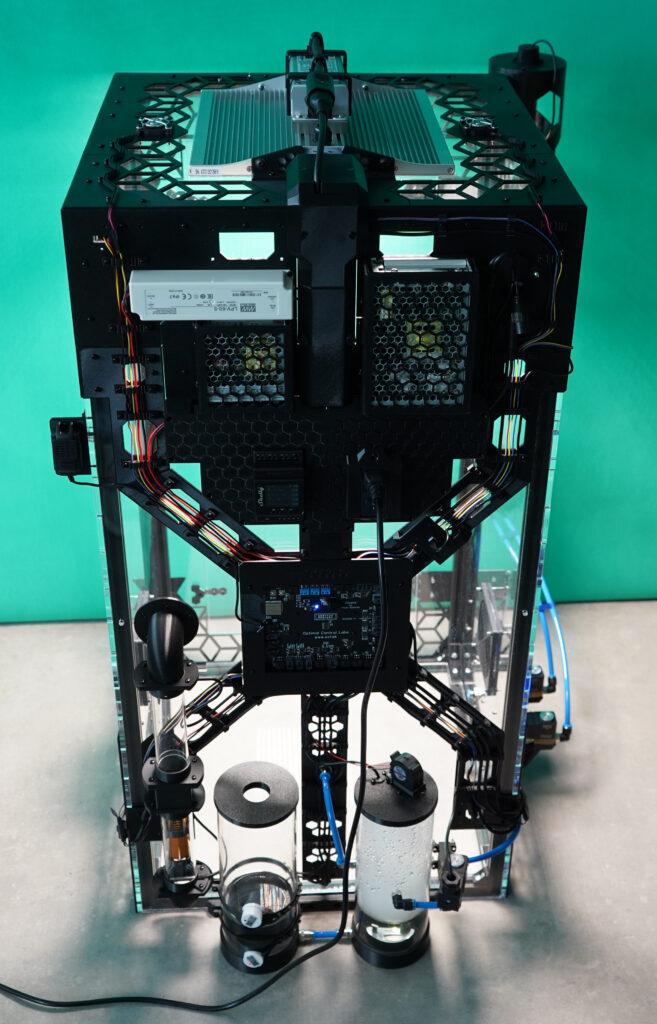
At the rear of the greenhouse, there are two other dynamic systems, one of which is the humidification system. This system is also relatively easy to control. The controlled variable in this system is the liquid level in two reservoirs, which interact with each other. The valve’s opening that refills water from the irrigation unit tank is the control variable. Therefore, the unit is fitted with two non-contact sensors to detect the liquid level. If the water level drops below its critical value, the top-up is activated. When the level rises above the critical value detected by the top sensor, the top-up ceases.
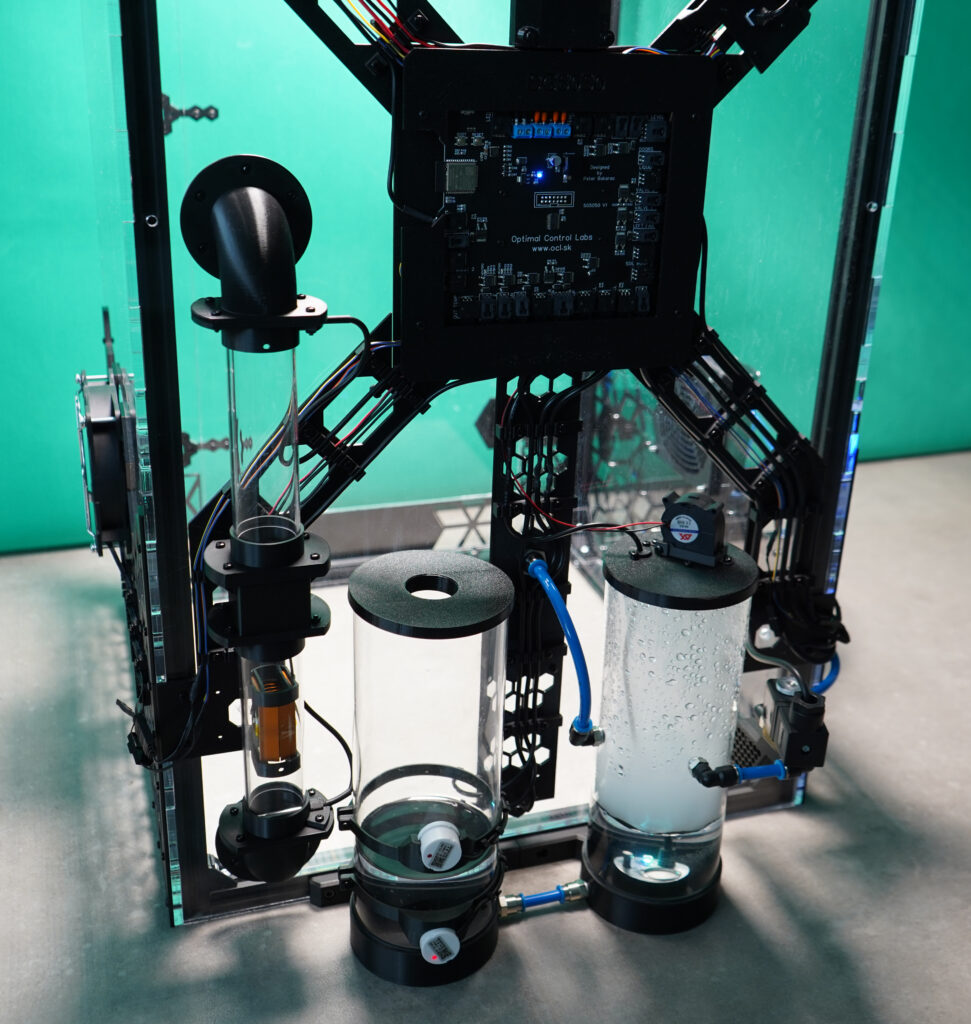
Furthermore, this unit acts as an actuator for humidifying the air inside the greenhouse. The mistmaker in the right tank generates mist, and the fan located on top of the tank blows air into it, pushing the mist or humid air into the greenhouse and increasing the humidity level.
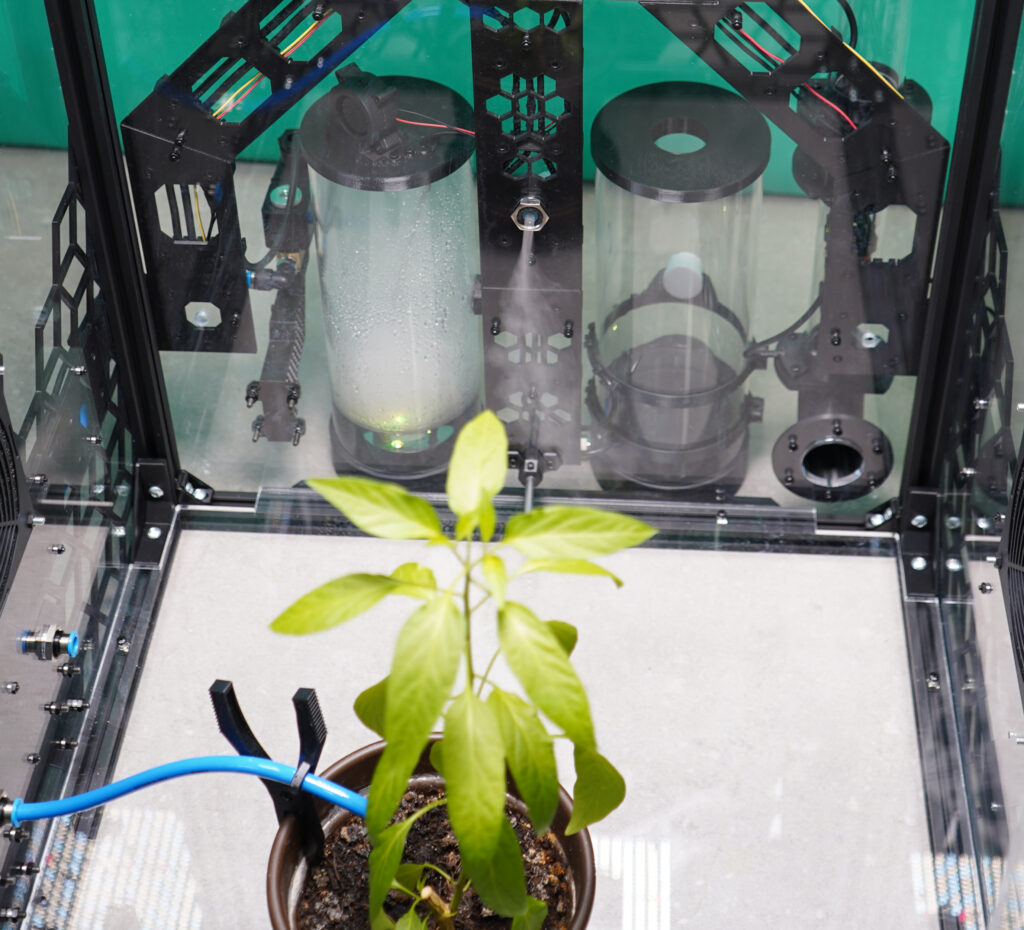
In addition to controlling humidity, maintaining the temperature inside the greenhouse is crucial for providing an optimal environment for plant growth. Various factors, such as ambient temperature and lighting, affect the temperature inside the greenhouse. To address this, an air heater is installed at the back of the greenhouse, alongside the humidification system. The air heater draws air from the middle of the greenhouse using a fan, heats it up, and returns it to the greenhouse at the bottom. The heater is powered by a pair of 20 W heating resistors, which can be controlled independently. A pair of thermometers measure the air temperature at the inlet and outlet of the heater. This system is more complex than the humidification system and is known as a MIMO (Multi Inputs – Multi Outputs) system.
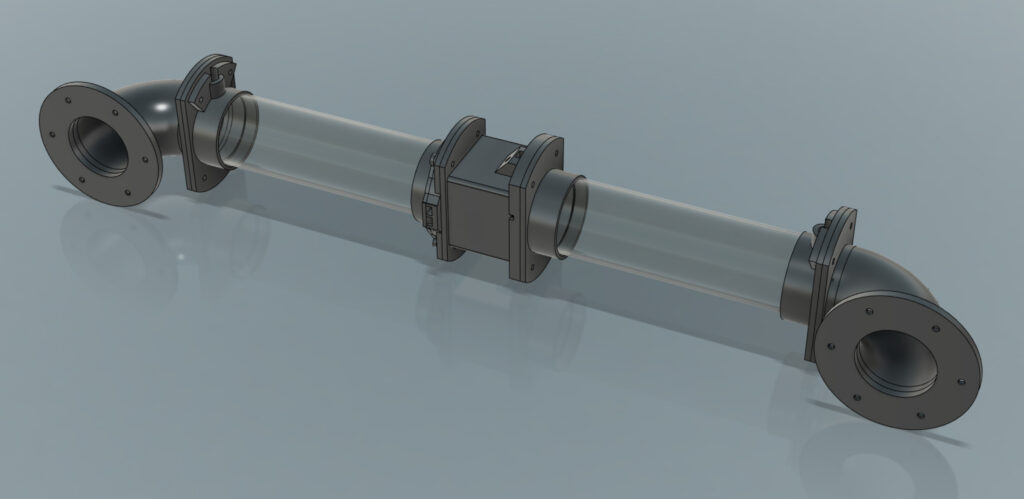
In a simple temperature control scenario, the temperature at the outlet of the heater is considered the manipulated variable, while the fan power and heating resistor power are the control variables. However, in a more complex scenario, the entire system must be considered globally. For example, if the fans on the sides of the greenhouse are turned on, they will pull ambient air in and out, causing a drop in temperature inside the greenhouse (if the ambient temperature is lower). In such cases, the heater must compensate for the temperature drop, and the control algorithm must take into account various factors, such as ambient temperature, greenhouse temperature, and heater inlet and outlet temperatures. The process becomes even more complicated if humidity must also be controlled alongside temperature.
In order for the control algorithms to reliably regulate the aforementioned variables in the indoor environment of the greenhouse, precise measurements must be taken by sensors. Therefore, the interior of the greenhouse is equipped with multiple sensors to measure temperature, humidity, and carbon dioxide (CO2) concentration. Temperature is measured at the bottom, middle, and top of the greenhouse, while CO2 concentration is measured in the middle. Additionally, temperature and humidity are measured around the greenhouse.
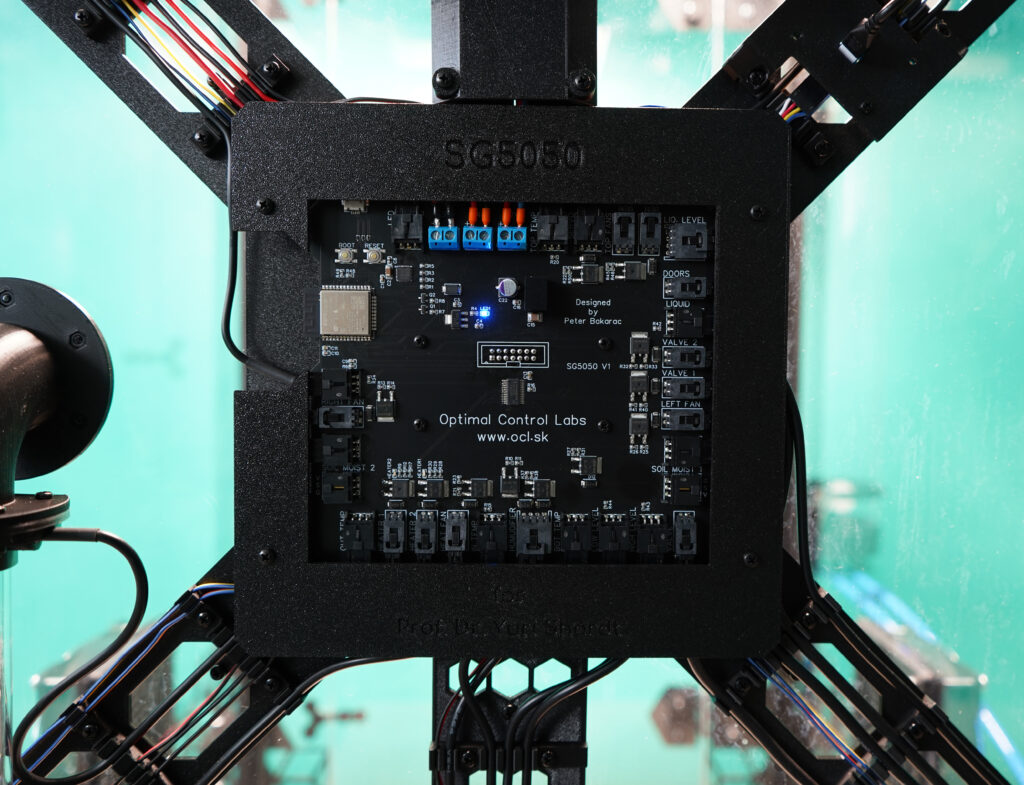
The latest innovation is the electronic control unit, custom-designed to include connectors for all actuators and sensors. It is based on the ESP32 microprocessor, which has a built-in WiFi or Bluetooth module. The system enables remote control, data collection, and archiving through the use of various cloud services. The data collected can then be utilized for the creation and design of machine learning algorithms, which are instrumental in predicting various events, such as a sensor or actuator failures, and identifying malfunctions.
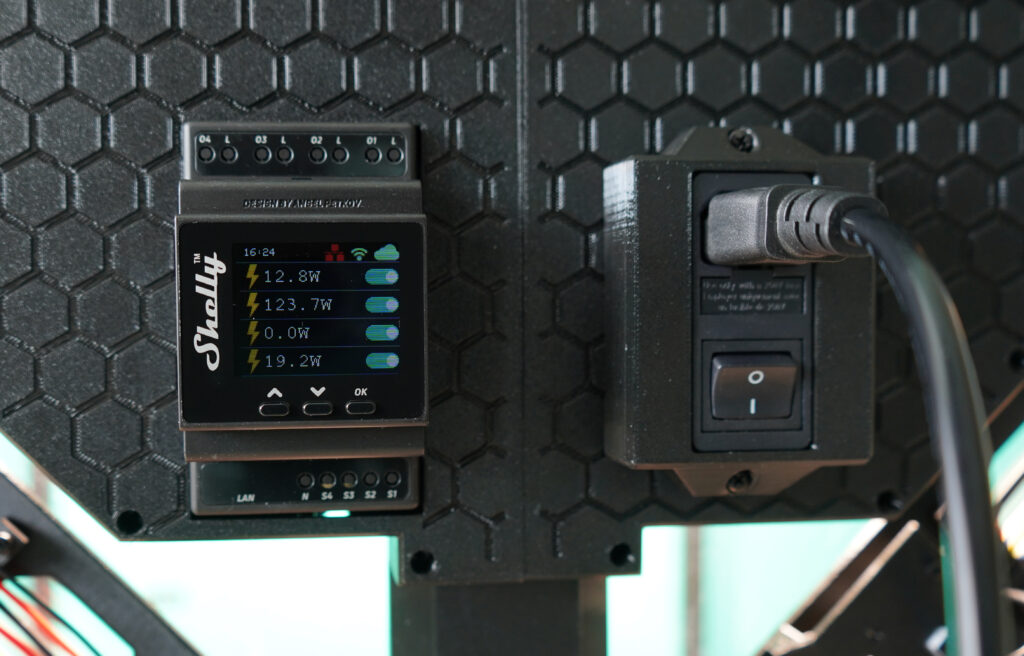
Additionally, the system is fitted with an intelligent power meter that provides an overview of the energy consumption of the individual components. As this project prioritizes ecological and environmental aspects, we find it essential to consider the energy consumption of the system. Therefore, we design our control algorithms to not only maintain optimal greenhouse conditions but also minimize energy consumption.
The greenhouse model was developed as part of an international collaboration for Prof. Dr. Yuri Shradt, who is affiliated with the Department of Automation Engineering at the Technical University of Ilmenau in Germany. We gratefully acknowledge his support.
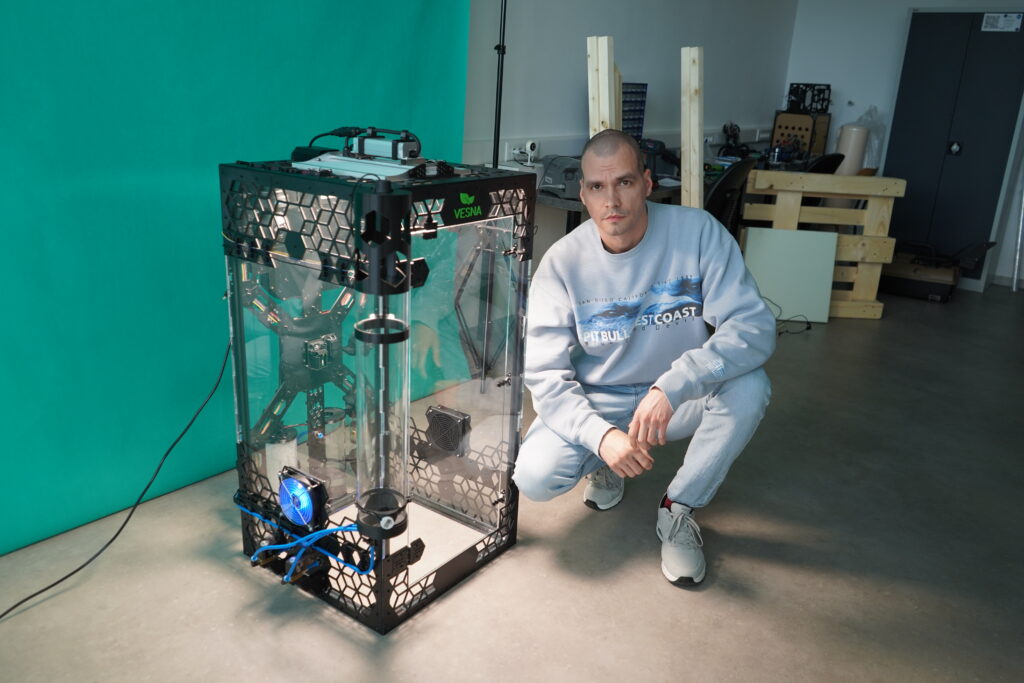